고위험 공정 첨단기술로 대체해 종사자 안전성 확보
고소작업·밀폐공간·화재 등 다양한 분야에서 활용
사업주·경영책임자 등의 안전보건조치 의무를 대폭 강화하는 것을 골자로 하는 중대재해처벌법이 내년부터 본격 시행되면서 주요 대기업들의 발걸음이 분주해 지고 있다.
최근 화두로 떠오른 ESG(친환경·사회·지배구조) 경영시스템에 안전 최우선 경영 방침을 포함하는 가운데 대대적인 투자를 통해 안전 중심의 조직 쇄신, 선진 안전보건경영시스템 구축 등에 열을 올리고 있다.
이러한 추세는 특히 안전관리 기술 분야에도 가시적인 변화를 가져왔다. 업종을 막론하고 많은 기업들이 4차 산업혁명시대 핵심 기술을 적용한 스마트 안전관리를 전개하고 있는 것이 그 예다.
이처럼 기업들이 스마트 안전관리에 심혈을 기울이는 이유는 간단하다. 사후대응이 아닌 사전예방에 방점을 두고 안전관리 패러다임을 전환하는 것이다. 최첨단 신기술을 도입해 안전하고 건강한 일터 조성에 앞장서고 있는 기업들의 사례를 정리해 봤다.
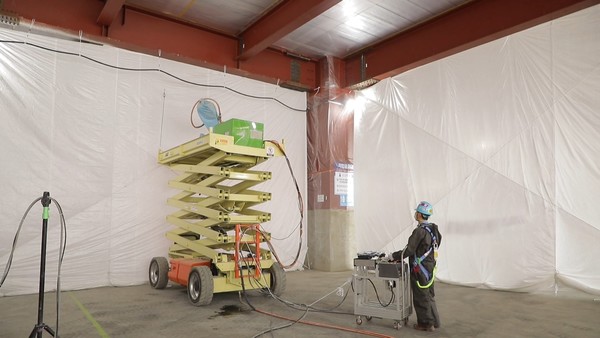
◇삼성물산, 내화뿜칠작업 로봇 도입
앞으로는 건설현장의 대표적인 고위험 작업으로 분류되는 ‘내화뿜칠’ 작업을 로봇이 하는 모습을 어렵지 않게 볼 수 있을 전망이다.
삼성물산 건설부문은 국내 최초로 ‘내화뿜칠’ 작업을 대체할 수 있는 기술을 개발하고 현장에 적용했다고 최근 밝혔다.
참고로 내화뿜칠 작업은 건축물에 화재가 발생했을 때 철골 기둥과 보 등이 높은 열에도 견딜 수 있도록 내화재(耐火材)를 덧칠하는 것이다. 문제는 이 작업 시 노동자가 유독성 물질에 노출될 우려가 높고, 고소작업이 필연적으로 수반돼 추락사고의 위험도 높다는 데 있다.
삼성물산이 개발한 내화뿜칠 작업 로봇은 고소작업대 상부에 내화재 분사를 위한 로봇팔을 적용하고, 하부에는 원료 혼합기와 저장설비를 일체화한 것이 특징이다. 특히 이동식 플랫폼이 적용돼 현장에서의 활용이 용이하다는 장점이 있다.
삼성물산은 이 로봇을 대규모 철골 기둥으로 이뤄진 반도체 공장 건설현장에 우선적으로 활용한다는 방침이다.
삼성물산의 한 관계자는 “건설 자동화 기술은 노동자의 안전을 지키는데 궁극적인 의미가 있다”라며 “앞으로도 작업자의 안전을 최우선으로 할 수 있는 기술 개발에 앞장설 계획”이라고 말했다.
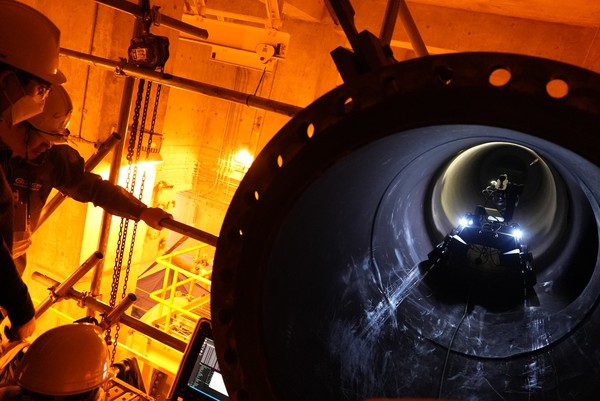
◇한국수력원자력, 해수 배관 내부 작업 로봇 ‘프라임’ 눈길
한국수력원자력은 고위험 밀폐공간 작업인 해수배관 내부 점검을 수행할 수 있는 지능형 로봇 ‘프라임(Prime)’의 시제품을 개발했다.
한수원에 따르면 기존 지하 배관 점검 시 내부에 작업자가 직접 들어가 육안으로 확인하고 타격을 통해 음향을 듣는 식으로 점검을 수행해 왔다. 이러한 방식은 배관이 지하에 있고 밀폐공간인 탓에 안전사고의 우려가 높다.
이를 개선하기 위해 개발된 지능형 로봇 프라임은 해수 배관 내부를 자율 주행하고 손상 여부를 확인할 수 있는 타격 동작도 직접할 수 있다. 또 인공지능(AI) 알고리즘을 활용해 타격 음향 분석도 가능하다. 한수원은 프라임이 수집한 카메라 영상, 3차원 표면 측정값, 음향데이터 등의 점검 결과를 가상의 3차원 배관 형상에 모사해 디지털 트윈 개념으로 구현하는 프로그램 개발에 박차를 가하고 있다. 이를 통해 향후 2023년까지 고위험 배관 점검 작업을 로봇으로 완전히 대체한다는 계획이다.
전혜수 한수원 디지털혁신추진단장은 “로봇 기술을 활용한 첨단 원전 운영기술로 국내 원전 및 종사자의 안전성 향상은 물론, 발전분야의 첨단 기술을 선도할 것”이라고 말했다.
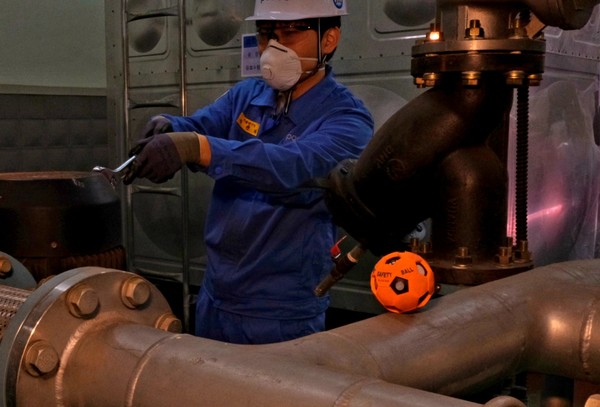
◇포스코, 유해가스 꼼짝마 ‘스마트 세이프티 볼’ 화제
밀폐공간 유해 가스 존재 여부를 사전에 탐지해 작업 종사자의 안전성을 확보할 수 있는 기술이 개발돼 화제다.
포스코는 세계 최초로 ‘스마트 세이프티 볼(Smart Safety Ball)’ 개발에 성공했다고 최근 밝혔다.
포스코에 따르면 기존 밀폐공간 작업 시 사전 유해가스 등의 측정을 위해서 긴 튜브를 사용하거나 작업자가 휴대용 감지기로 직접 측정을 하는 불편이 있었다.
하지만 이번에 개발된 스마트 세이프티 볼은 직경 60mm, 무게 100g의 테니스공과 비슷한 크기로, 작업 공간에 투척만으로 가스 농도 등을 실시간으로 측정할 수 있다. 산소(O₂), 일산화탄소(CO), 황화수소(H₂S) 등 3가지 가스 농도 파악이 가능하며, 측정된 값은 스마트폰이나 태블릿PC 등 전용 앱에서 실시간으로 확인할 수 있다.
특히 위험 수준의 농도가 감지되면 사전에 등록된 동료와 관리자에게 메시지와 위치정보가 전달돼 비상 시 신속한 조치도 가능하다.
또한 장애물이 없는 평지에서는 통신거리가 최대 100m이고, 장애물이 있거나 밀폐된 곳에서도 30m 내외는 신뢰도 높은 측정을 할 수 있다. 이외에도 내장 배터리로 2년간 상시 작동되며 방진, 방수 기능은 물론 측정 센서가 항상 상부를 향할 수 있도록 하부에 무게 중심을 갖춘 오뚝이 기능도 구비하고 있는 것이 특징이다.
포스코는 우선 일부 부서를 대상으로 스마트 세이프티 볼을 시범 적용하고 상반기 내에 법적 인증까지 완료한 후 제철소 내 관련된 전 공장을 대상으로 적용·배포할 예정이다.
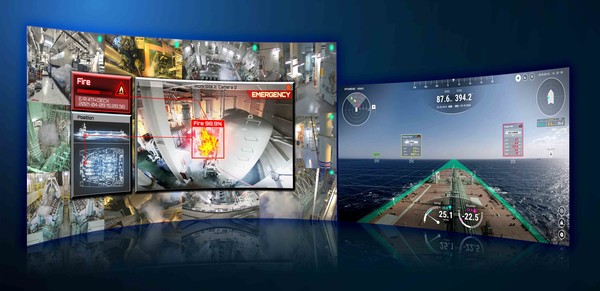
◇현대중공업그룹, 인공지능(AI) 기반 선박 화재 감시 시스템 개발
인공지능을 활용해 선박 내 화재를 실시간으로 감지하는 시스템도 개발됐다.
현대중공업그룹은 조선업계 최초로 인공지능(AI) 기반 안전관리시스템(HiCAMS)을 개발해 한국선급과 라이베리아 기국의 기본승인(AIP)을 획득했다고 최근 밝혔다.
이 시스템은 AI를 활용해 선박 내 화재를 감시하는 영상 분석 기반의 안전 솔루션이다. AI가 엔진룸 등 선박 내 기계 구역에 설치된 20여대의 CCTV 영상과 화재 빅데이터를 분석, 화재 초기 단계에서부터 불씨와 연기 등을 포착할 수 있다는 게 특징이다.
특히 이 시스템에는 스스로 데이터를 쌓으며 학습하는 딥러닝 기술이 적용돼 기존 화재 감지센서에서 빈번했던 오경보 작동 등도 제거할 수 있다는 장점이 있다. 또한 화재 징후를 실시간으로 탐지함에 따라 기존에 2분 가량 소요되던 화재 인식 시스템의 문제점도 개선됐다.
현대중공업그룹은 향후 선박 전체로 이 시스템을 확대 적용해 안전관리를 강화해 나갈 예정이다. 아울러 화재 감시시스템을 시작으로 누유, 누기, 인명사고 등에 대한 안전관리 시스템도 개발해 AI 기반의 통합 선박 안전솔루션도 구축할 계획이다.
현대중공업그룹의 한 관계자는 “조선업계 최초로 선박 안전관리 분야에 AI를 접목했다는 점에서 의미가 있다”며 “AI 기술을 선박 안전분야 전체로 확대 적용해 미래 무인선박 시대를 선점할 것”이라고 밝혔다.
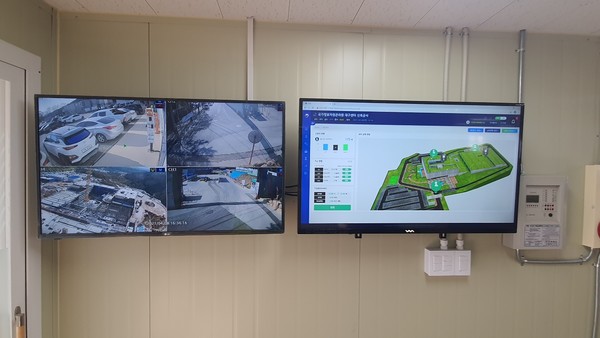
◇현대건설, IoT 기반 플랫폼으로 현장 위험요소 사전감지
건설현장에서 코로나19 등 감염병 위기 사태를 비롯해, 침수, 화재 등 각종 재난에 신속하게 대응할 수 있는 플랫폼도 운영된다.
현대건설은 자체 안전 관리 플랫폼 ‘하이오스(HIoS)’에 감염·침수·화재 사고 대응 기능을 추가한 안전 서비스를 현장에 제공한다고 최근 밝혔다.
앞서 현대건설은 지난 2019년 건설사 최초로 전사적인 차원의 안전관리 플랫폼인 하이오스를 도입하고 작업자 위치관제, 밀폐공간 가스누출감지, T/C충돌방지, 환경민원관리 등의 현장 안전서비스를 제공해 왔다.
이번에는 사물인터넷(IoT) 기술을 바탕으로 감염병, 화재사고, 침수 등에 대한 사전 감지 기능을 추가적으로 보완했다. 현대건설은 이번 기능 보완을 통해 노동자들의 감염병 징후 등 각종 건강이상을 비롯해 침수, 화재 등 현장의 위험요소에 대한 신속한 대응 조치가 이뤄질 것으로 전망하고 있다.
현대건설은 현재 스마트건설 혁신 현장인 ‘대구 정부통합전산센터’에 추가 기술을 통합 적용했으며, 향후 다른 현장으로도 확대해 나간다는 방침이다.
현대건설의 한 관계자는 “하이오스(HIoS)에 저장되는 노동자 위치 및 센서 데이터를 기반으로 빅데이터 분석을 지속적으로 수행해 글로벌 건설사 위상에 걸맞은 스마트 안전관리를 전개해 나갈 것”이라고 말했다.