AI 기반 영상인식·알고리즘 개발…선적·하역작업 안전 확보
데이터 시각화로 크레인 운전자 불안전 상태 즉각 감지
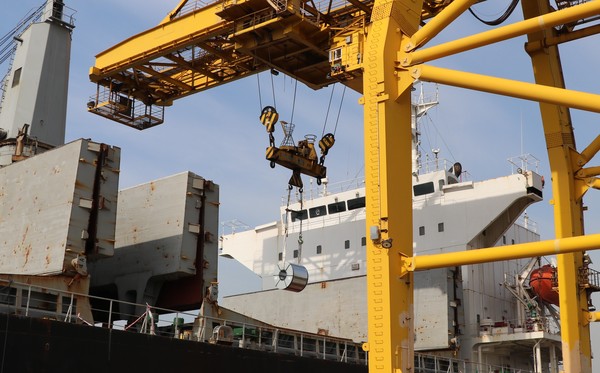
포스코가 ‘크레인 안전거리 자동측정 시스템’을 개발해 충돌과 낙반 사고에 노출된 크레인 작업환경의 위험요소를 스마트하고 안전하게 바꿔나가고 있다.
11일 포스코에 따르면 이 시스템은 인공지능(AI) 영상인식 및 알고리즘을 기반으로 크레인 상부에 설치한 카메라 및 센서에서 수집한 높이, 거리 등의 데이터를 종합, 선적·하역 작업 시 안전거리를 자동 측정해 충돌을 예방하는 시스템이다.
기존에는 크레인 운전자가 적정 선적·하역 높이를 육안으로 확인해야 했다. 특히 해수면 변동 및 시야 확보 제약 등이 있을 경우에는 측정하는 데 많은 어려움을 겪었다. 하지만 이 시스템은 측정한 데이터 값을 시각화해 운전자에게 실시간으로 적정 선적·하역 높이 및 작업 위험요소를 크레인 내 모니터에 표시해준다.
포스코의 제품부두는 철강코일 등 무겁고 특수한 제품을 선적·하역하는 작업 특성상 면밀한 안전관리를 필요로 한다. 이 때문에 크레인 안전거리 자동측정 시스템의 활용도가 높다.
예를 들어 낱장 단위로 선적을 해야 하는 후판은 폭과 길이가 다양해 줄걸이를 수작업으로 체결해 선적하다보니 제품 이동 중 기울기 변화 등으로 인한 낙반 사고의 우려가 있었다. 하지만 해당 시스템을 적용한 뒤 선적 과정 중 제품의 기울기 변화와 줄걸이 장력을 실시간으로 측정해 균형이 흐트러지면 즉시 모니터에 시각화하고 자동으로 경보가 울려 사고를 예방할 수 있다.
향후 포스코는 크레인 안전거리 자동측정 시스템과 같은 인공지능을 탑재한 스마트 안전기술을 지속적으로 개발해 더욱 안전한 제철소를 구현해 나간다는 방침이다.
기술 개발에 참여한 송은하 광양제철소 생산기술부 대리는 “크레인 안전거리 측정 시 실시간 해수면 변동, 선적 시 제품 하중 증가로 인한 선박 수위 변화 등 변수가 많아 시스템 개발에 어려움이 많았다”며 “안전이 최우선인 제철소 작업환경을 구축하는 데 작게나마 역할을 한 것 같아 자부심을 느낀다”고 밝혔다.
한편 포스코는 지난 4일 시행된 항만안전특별법에 맞춰 안전관리를 강화하고 있다. 지난 3월에는 제품 부두 내 추가 작업공간을 확보하고 코일 전용 화물운반대에 안전보강 설비를 설치해 추락을 방지하도록 했다.